- Offset Ink
- Gravure Ink
- Metal Ink
- UV Ink
- Flexo Ink
Inks that are transferred onto a flat plate then transferred from the blanket to the substrate (paper, metal, film...) using any printing method are commonly called offset ink.
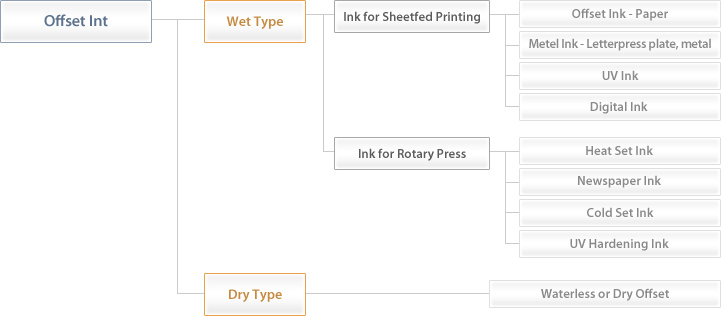
- Used for sheetfed printing
- Relatively high viscosity with high pigment and resin content
- Able to produce high quality printing jobs on a variety of surfaces
- Used for mid-low speed (8000~15,000 sheets/HR) printing machines
- Rapid conversion from photocopiers for small quantity printing to digital printing machines for small impressions, copier and digital imaging printer replace convential offset printing press
Type | Type of Paper Used | Feature |
---|---|---|
Matt paper | Art paper, Double coated paper | Quick setting high gloss |
General Use | Matt Art paper, Imported paper (high pulp content) |
Resistant to chalkingHigh resin content, high contrast |
Duplex Board | Duplex Board, Cardboard box | Excellent resistance to abrasion, high density, very durable |
Unabsorbent paper | PVC, gold/silver foil, currency notes | Low solvent content |
Unabsorbent paper | Tissue paper, dictionary paper | Low tack, low viscosity, low cost of raw materials used |
- Suitable for printing on roll paper
- Used for high speed rotary press (500 ~ 1600 rpm)≒30,000~100,000 m /hr
- Comparatively low viscosity and low T.V
- High speed, rapid expansion with low printing costs (penetrate offset market)
- Stable at high speeds (heat / weather conditions)
- High resistant emulsification
Type | Type of Paper Used | Feature-1 | Feature-2 |
---|---|---|---|
HEAT SET | Art paper | Top grade rotary ink, Ultra gloss | Bake dry (forced solvent evaporation) Solvent segregation QUICK SET |
Uncoated paper | Mid-grade rotary ink, High density | ||
COLD SET | Uncoated paper | Low cost Short term stability | Dry by permeation (SETTING) |
Ink is poured into concave (engraved) cells then transferred directly onto the substrate.
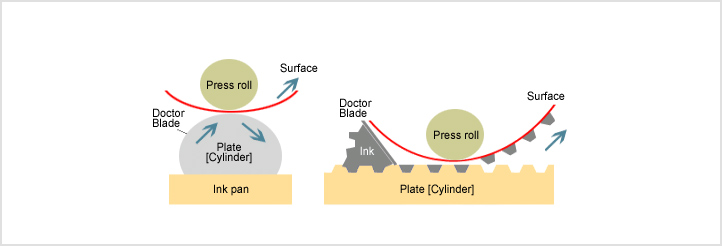
- Appearance : colored liquid
- Viscosity : (Zahn cup #4 : 10~20sec)
- Odor: (solvent type) smells like organic solvent
- Fire prevention: (solvent type) 4th dangerous item and 1st type of oil
Constituent | Content (wt %) | Phase | Functionality |
---|---|---|---|
Pigment | 5~40 | Powder | Color. Resistance to heat, light, acid, alkali, migration |
Resin | 0~20 | Derivative of solid viscosity | Adhesion. Post process procedures. Pigment dispersion. Film properties. |
Solvent | 40~85 | Liquid | Resin soluble. Adjust dry speed and viscosity. |
Compound | 1~5 | Liquid Solid, Powder | Improve print film properties |
- Use: food, industrial
- Printing Method : exterior surface printing, interior surface printing
- Substrate : Film, paper, Aluminum foil, steel, AL
- Resin : Urethane, NCPolyamide, Vinyl
- Solvent : solvent, non Toluene, water based
- Printing : cylinder contamination, metastatic, electrostatic field, blocking ability
- Post process : Laminate, Boil, Retort, etc.
- Substance resistance : soup base, repellant, etc.
- Film properties : scratch resistant, heat resistant, oil resistant
Film | Notation | Characteristics | Use |
---|---|---|---|
Polyethylene | PP | Better solidity, tensile strength and transparency than PEMoisture and OPP are highly resistant to aromatic gases and are not readily heat seal-able |
Cellophane replacementBottle caps, laminated products. After weaving, for woven bags |
Polystyrene | PS | Molds well with Blowing, Injection, Extuding Resistance to heat conduction becomes high EPS when heated in moisture. |
Dairy products, fish, meats, vegetable containers. EPS for buffers. Boxes used as food containers. |
Polyesters | PET | Good mechanical strength, high resistance to heat (300℃), blocks gas moisture, good resistance to organic solvents. Not heat seal-able. Better blockage with PVDC coatings |
Vacuum packing (Al foil, PE) Food,coffee packaging as well as bottling |
Polyamide(Nylon) | PA | Good mechanical strength and resistance to heat. Weakens in moisture. |
Packaging processed meats & fish |
Polyvinyl chloride | PVC | Strengths include good transparency and blockage of moisture, gas, fatty oils. Less stable with temperature change so a stabilizer is used when molding. Tin-containing materials and monomers are closely controlled. |
Rigid: mineral water, cosmetics, juice containers Flexible: Stretchable packaging, shrink-wrap |
Polyvinyidene chloride |
PVDC | Produced under the Saran brand name. Excellent resistance to chemicals, moisture, oxygen, carbon gas |
Vacuum packing, heat seal- able, high frequency, impulse adhesion is possible for foods and drugs |
Cellophane | PA | Produced under the Saran brand name. Excellent resistance to chemicals, moisture, oxygen, carbon gas |
Cigarettes, dry goods, packaging materials |
Cellulose Acetate | CA | High transparency | Envelope and box window Skin, Blister packaging materials |
Film Name | Inflammability | Odor | Color of flame/smoke |
Changes during combustion |
Condition after combustion |
---|---|---|---|---|---|
PE | O | Paraffin smell | Yellow on topBlue, black base |
Melts and falls off then burns |
Melts, hardens, black |
PP | O | Weaker paraffin scent than PE |
Blue topBlue base | Same as PE | Same as PE |
PVS | X | ||||
PS | O | Acrid chlorine smell |
Yellow flameGreen base | Softens and leaves soot | Softening black |
PS | O | SM smell | Yellow Black smoke | Melts and falls off then burns |
Melts, releases carbon after hardening, black |
Nylon | X | Smells of wool, nail |
Blue flame while yellow on top |
Melting drops fall but do not burn readily |
Melts, hardens into a camel color |
PET | △ | Distinctive odor | Yellow top, bluish green baseBlack smoke |
Shrinks while melting and leaves soot while burning |
Melts, hardens, black |
Cellophane | O | Smells like paper | Reddish yellow flame | Burns like paper | Leaves ashes |
- Reinforce durability : prevent product damage
- Protect contents : resistance to moisture and oil, prevents gas permeation
- Workability : adaptable to automated machines, heat seal-able
- Increase sales effect : presentable exhibition quality
- Consumer response : easy to use
- Wet Lamination(W/L) : A water-soluble adhesive is applied over the surface once moisture is able to permeate and evaporate through one side of the surface, then dried.
- Extrusion Lamination(EL or PEEL) : Printing film is fused together with a film made by fusing thermoplastic resin with heat.
- Polyethylene is commonly used for this process but AC agents may be used to reinforce adhesion. Titanate, Imine, Isocyanate may be used as anchor coatings.
- PPEL(Polypropylene Extursion Lamination) : Similar in theory to PEEL but is more transparent and has a higher melting point than PE. Intense PP and AC agents are not used, thus called AC-free PPEL. As it does not contain AC, it requires heatproof ink and the surface must be matted.
- Dry Lamination(D/L) : Apply an adhesive onto the substrate or film, evaporate the solvent using a drier, then apply pressure to fuse into a 2-component adhesive. Benefits include a wider selection of materials, less heat loss compared to PEEL, processable by retort boiling depending on the type of fused film, and resistance to elements including heat, cold, chemicals, etc.
- NSDL(Non Solvent Dry Lamination) : To handle the solvent residue problem, an adhesive is heated to lower its viscosity then applied and fused while moisture is blown in to harden. Take caution, as it is sensitive to the extent of curing.
This ink is used to print on various metal plates. It is available as a 3pc ink, which is used in the same manner as offset printing, and a 2pc ink, which is used in the same manner as letterpress flexo printing.
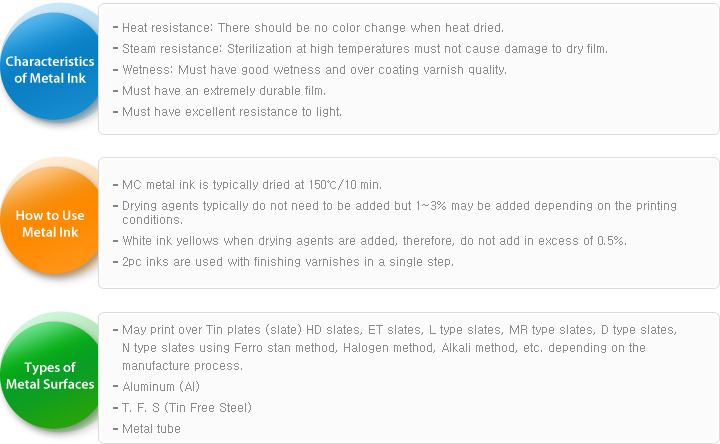
TThis ink is used to print on various metal plates. It is available as a 3pc ink, which is used in the same manner as offset printing, and a 2pc ink, which is used in the same manner as letterpress flexo printing.
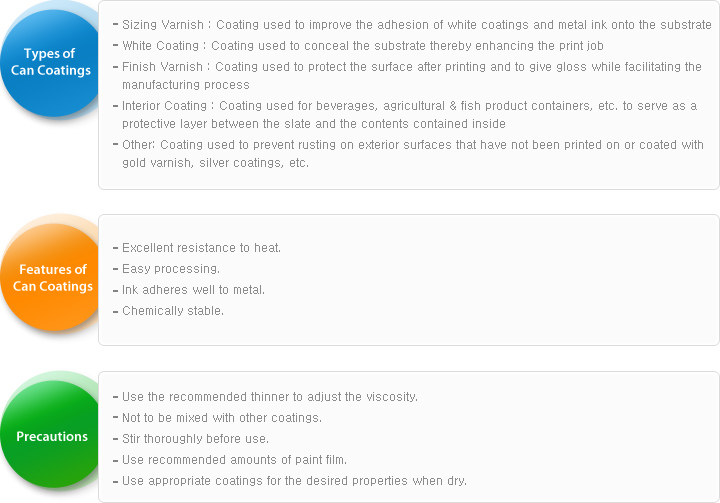
The "UV" in "UV hardening" is the abbreviation for Ultra-Violet, which refers to UV rays. "UV hardening" refers to the use of UV irradiation equipment etc. to cause hardening in a relatively shorter time period compared to natural chemical processes.
- Ancient times: Bitumen on mummies were wrapped in hemp cloth that was daubed with lavender oil, then hardened under sunlight (1st record)
- 19th century: Ink made from unsaturated vegetable oil was applied then hardened under sunlight 40~50's: Introduction of a rapidly hardening method using a UV ray lamp (1st UV hardening ink patented in 1946)
- 60's: Environmental legislation, oil fluctuations and increased productivity as a result of rising demands accelerated the development of UV hardening resins (German company, Bayer's UV hardening unsaturated polyester coating product in 1969 - 1st industrial use of UV)
- 70's: Started application of coatings for wood? Expanded area of application with the development of an acryl type UV ink by the American Company, SUN Chemical, INMONT. In 1975, or thereabouts, BASF, Bayer developed an unsaturated polyester UV coating for application on wood, however, active research of UV resins in America contributed towards application in all areas.
The "UV" in "UV hardening" is the abbreviation for Ultra-Violet, which refers to UV rays. "UV hardening" refers to the use of UV irradiation equipment etc. to cause hardening in a relatively shorter time period compared to natural chemical processes.

Electromagnetic rays having wavelengths in the 10 ~ 400nm range are called UV rays, which are broken down as follows
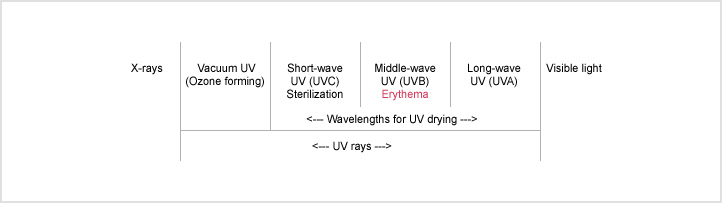
PROS | CONS |
---|---|
Hardens at low temperatures | Constrained by the formation of waves |
Hardens quickly | High cost of coatings & ink |
Excellent paint properties & hardening characteristics | Coatings & inks cause skin irritation |
High solid content | - |
Simple to manage process | - |
Low energy cost | - |
Prevents air pollution | - |
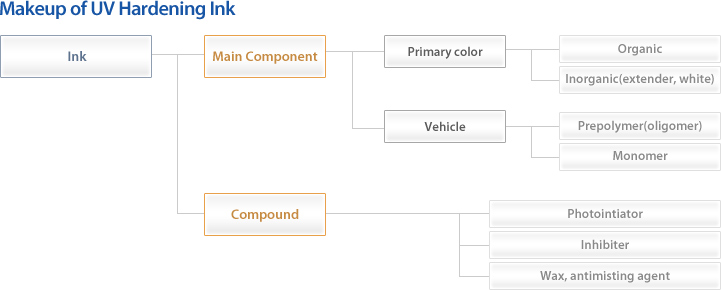
UV hardening coatings & inks harden with the activation of photoinitiators that decompose with UV energy to form radicals that induce reaction. This activator causes monomers & oligomers, etc. to sequentially undergo reaction generally in 3 stages.
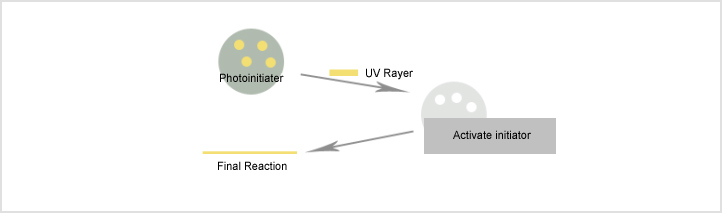
UV coatings & inks are used nowadays in the following areas. Clear coatings are generally used but lately with the development of colored UV coatings & ink, the areas of application are continuously expanding.
- wood : filler & sanding sealer
- plastic: PVC floor coatings, wall coatings
- metal : rustproof basecoat on steel
- paper : various packaging materials & Over Coating
- adhesive : laminate adhesion of transparent film
Apart from the coating & ink areas mentioned above, with the popularization of UV hardening systems, it may extend into electronic parts that focus on print circuit boards.
- Ink may not readily transfer when first switching from common oil ink to UV ink. Rollers must be cleaned with UV cleaning liquid before use.
- Adhesion of UV ink varies depending on the substrate, so adhesion must be checked prior to any application.
- Take precaution, as UV ink varies much more in viscosity with temperature compared to common oil ink.
- When offset printing on unabsorptive surfaces, water cannot permeate through the surface. Using large quantities of water will give poor adhesion so it is best to use little water when printing.
- Any cleanser left on printing machines may slow dry time so it is best to print when there is no cleanser remaining.
- Hardness must be checked when printing. Hardness varies depending on the color and concentration of UV inks.
Flexographic Printing is a printing method that uses a flexible & elastic rubber or resin letterpress and ink that dries with the evaporation of organic solvents made of water or alcohol based esters.
Analine prints were introduced with rotary printing of labels or trademarks on packaging machines using analine colorants on rubber plates. This was improved using colorants, one of the raw materials, and a synthetic resin vehicle to develop an area of printing that was named flexographic printing. Through the improvement of various areas, this handy printing method tackles drawbacks with benefits such as high energy efficiency, non-pollution, economic efficiency, high speed, etc.
Characterized by using a plate made of flexible matter that is processed by letterpress flexo.
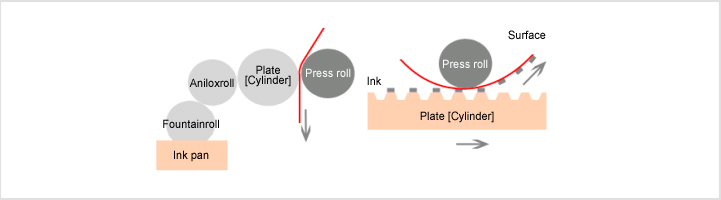
- Photoengraving is simple at low cost.
- Plates are easily reproduced and parts may be replaced.
- Suitable for small-scale printing.
- Post process treatments (hole perforation, molding wax synthesis, other (iron mounting)) may be carried out immediately afterwards.
- Uses water-based (water, alcohol) solvents, which makes it environmentally friendly
- Appearance: colored liquid
- Viscosity: (Zahn cup#4: 10~20sec)
- Odor: water based → smells of Ammonia; oil based → smells of organic solvent
- Fire Prevention: (solvent type) 4th dangerous item and 1st type of oil
Type | Characteristic | Use |
---|---|---|
Alcohol | May apply on a wide range of boards as it contains Ethanol, IPA or other Glycol that cause minimal effect to the plate. Tendency of absorbing moisture. |
Al exterior printing OPP, PE exterior surface printing |
Co-Solvent | Must use a synthetic resin plate that is highly resistant to solvents as it contains alcohols & esters. Makes a wider variety of resins available. |
Application on Al-foil, Polyolefin, Polyester Nylon, etc. Interior/exterior printing |
Water | Inflammable with no solvent residue. May be diluted with water. Harder to re-fuse. Limited dryness. |
Paper |